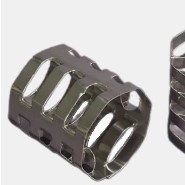
Features:
High resistance to corrosion:
in chloride environments such as seawater.
to the action of acids such as sulfuric, nitric, phosphoric.
to pitting corrosion.
to intergranular corrosion.
Resistance to sensitization: AISI 316 Ti has better...
Read more →
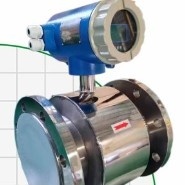
Electromagnetic flowmeters are widely used to measure various conductive liquids in industry. For example, the measurement of corrosive liquids such as sulfuric acid, sodium hydroxide, nitric acid, hydrochloric acid, seawater, sewage, various acids, alkalis and salts such as hydrochloric acid, acetic acid and hydrofluoric acid, various industrial wastewater, paper pulp. Tap water, drinking...
Read more →
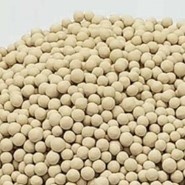
13X molecular sieve , also known as 13x zeolite, is a kind of synthetic zeolite with a specific pore size and structure that makes it highly effective for a variety of applications.
Here are some common uses:
1. Gas separation and purification:
used to separate nitrogen from oxygen in air separation plants;
natural gas processing: removes water, CO2 and other...
Read more →
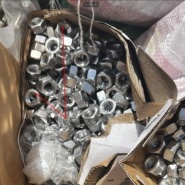
For the rectification column 1400 mm supplied valve plates of 3 mm stainless steel and 2 mm valve of 321 steel. Considering the slight difference in chemical composition, AISI steel 321 and its analogue 12Х18Н10Т belong to the categories of non-magnetic heat-resistant and heat-resistant alloys.
All parts and fasteners are also made of 321 steel
Our technological...
Read more →
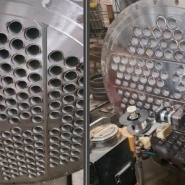
Shell-and-tube heat exchangers for acute and recovery steam in the production of alcohol and bioethanol.
Read more →
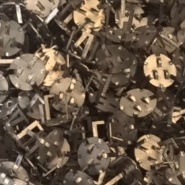
Production of valves for a distillation column made of 08Cr13 steel with a thickness of 2 mm.
Rectification columns are used to separate oil into fractions during distillation.
The internal devices of the plate and the column body are made of heat-resistant stainless steel.
Our company manufactured valves for the distillation column from 08Cr13 steel, a 2 mm thick...
Read more →
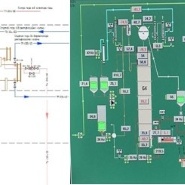
The use of energy resources at enterprises producing ethanol, in particular “heat” and “cold,” play an important role in determining the cost of production and the price of the finished product.
The most effective method of heat recovery is “heating” the distillation column (DC) with alcohol steam from the distillation column (RC). This method works as follows: alcohol steam from the...
Read more →
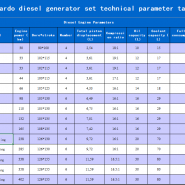
Ricardo diesel generator models are a high power power plant equipped with a professional diesel engine.
It can be used as the main or backup source of energy in everyday life, in emergency services, in construction, in hospitals, gas stations, etc.
Ricardo is able to work up to 24 hours without refueling and stopping, depending on the consumption and power of the model....
Read more →
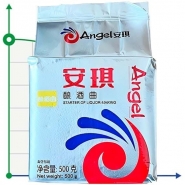
General characteristics of yeast
Saccharomyces cerevisiae is a type of alcoholic yeast . Like all substances of this type, Saccharomyces cerevisiae are
unicellular microorganisms of the class of ascomycetes or marsupial fungi. They are used to start the process of
fermentation of sugar and its gradual transformation into alcohol. Saccharomyces cerevisiae reproduce by budding. If...
Read more →
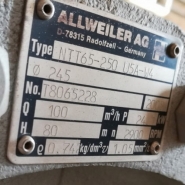
Hot superheated oil pump replacement with BTKF-K 65-250 analog (3000)
The dimensions and dimensions are suitable in order not to alter the pipe binding and meet the basic characteristics.
In this pump, we have an impeller diameter of 245 mm, and the replacement of the BTS Engineering pump offers a wheel in a 242 mm configuration, which is not particularly important when...
Read more →
33 posts